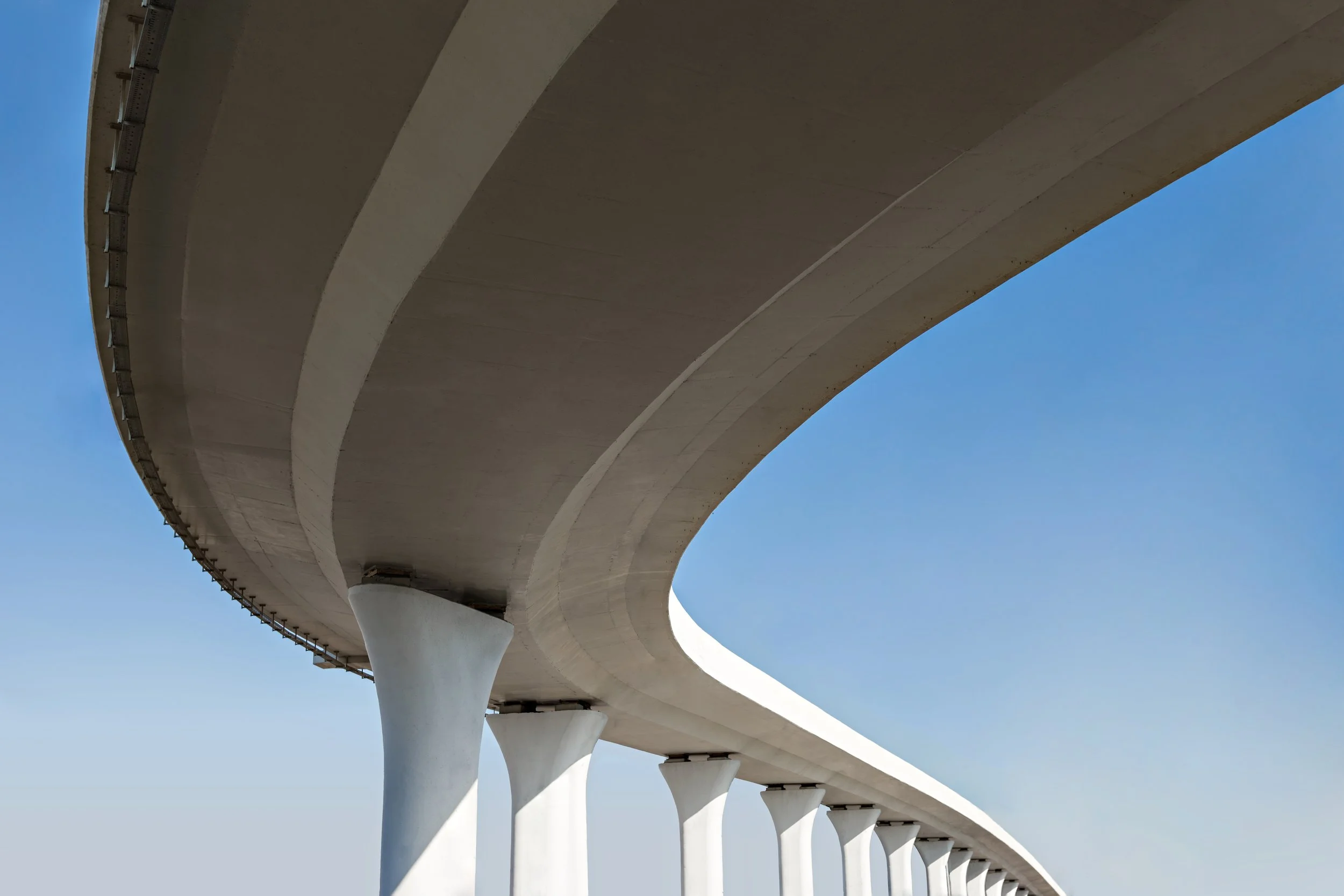
Frequently Asked Questions
The following FAQ provides deeper insight into the operation and capabilities of IPR Sensing Structural Health Monitors.
-
SHMs are designed to become the “voice” of a structure to report health status and concerns. As the major task of any structure is to safely bear a load, the SHM monitors a range of parameters that can affect that capability such as structural stresses, vibration, temperature, and humidity.
-
There are 3 main reasons. First, it is more efficient and cost-effective to bundle multiple sensors alongside common elements such as a power supply and local processing within a single installable package. Second, the power consumption in the case of battery powered SHMs can be significantly reduced with all sensors residing in the same package. Third, having all sensors in one package assures that all data is coming from the same physical location.
-
For sensing strains, the installation is as simple as installing a conventional strain gauge. Typical surface preparation steps include removing paint and sanding and then cleaning the surface using Acetone and Isopropyl Alcohol. The SHM is affixed using fast curing adhesives. Optionally, the SHM can be sealed with conventional sealants.
For applications requiring vibration and environmental measurements, SHM installation is even easier, using removable double-sided adhesive tape. Due to the very low weight of the SHM (4 grams), the effect of elasticity of the adhesive tape on the sensing accuracy of acceleration is negligible.
-
The SHM can be powered by any battery providing voltage from 2.3 to 5.5 V and at least 2.5 mA of current. The IPR USB battery module uses two 3.6 V SAFT LS14250 lithium ion batteries with a combined capacity of over 2400 mAH. That is sufficient to drive the SHM at full processing power for 1200 hours. Using smart ON/OFF functionality, the SHM can save battery power when no events of interest are present. In sleep mode the SHM consumes less than 50 uA. Thus with a duty cycle of 10% the batteries will last for approximately 13 months. With a duty cycle of 1% (about 15 min of active operation per day), the batteries will last for approximately 4 years.
-
In addition to providing extended run-time, the SHM has an internal real-time clock (RTC). To preserve the clock setting, batteries are replaced one-by-one so that the power to the RTC is uninterrupted.
-
The SHM can run in either autonomous mode or in data streaming mode.
In autonomous mode, the SHM accumulates data locally that can be collected either by direct cable connection (e.g. USB) or through a companion wireless module. The SHM is engineered with onboard data processing algorithms to distill the raw sensor data into a compact format for efficient accumulation and retrieval.
When the SHM is in data streaming mode, the SHM is directly connected to a host computer by USB which provides continuous power and the option to collect data periodically or continuously.
-
The SHM comes with full data encryption and the access to the RF link is also password protected.
-
There are RF transceiver variants – amplified, and non-amplified. The non-amplified variant has a line-of-sight range of about 300 m. The amplified variant has a range of 2-3 km. The range greatly depends on the shielding effects of the structure. For example, a heavily EM-suppressed environment can reduce the range of RF transmission to 20-50 m for the amplified version of the sensor. Interference is another factor to consider. In a dense urban environment, the reliability of the RF link can be problematic.
-
Yes, but we do not provide a system that can guarantee this connection. Instead, the SHM is designed to work autonomously during flight and transfer data after the aircraft lands. For that mode of operation there are algorithms that determine when the plane is stationary and the RF module is given permission to “listen” only. After receipt of a secure request from the ground-based RF module, communication can be established and data transferred.
-
The SHM can operate from -60C to +115C. Note that the selected batteries must support at least 2.5 mA of current and 2.3 V minimum voltage across the expected operating temperature range.
-
For aerospace applications barometric pressure is needed to assess the altitude of the aircraft independently from the aircraft avionics and sensors. Typically, the altitude will be used in detecting the “ in flight” or “no flight” condition and, accordingly, turn the SHM on or off to preserve the battery. Another use is in the assessment of environmental conditions affecting the structure, and in particular, corrosion damage.
-
The SHM can be programmed to execute a theoretical corrosion assessment protocol based on a history of readings from relative humidity and temperature sensors and correlation of those environmental factors with rates of corrosion for a given material and its protective layers. (e.g. paint, anodization, galvanization etc.)
-
The SHM housing is not fully hermetic. One reason is that barometric pressure and relative humidity sensors require an opening or passage from the SHM to the ambient atmosphere. However, for water-tight applications the SHM can be fully encapsulated after its installation using Silicone sealant. The SHM cable insulation is also made of Silicone rubber and when sealed provides for water tightness.